RISE researchers have developed a new low-cost method for manufacturing nanocellulose films, based on the Digital Cellulose Center’s research. The bio-based material can replace plastics in many products as well as be used in energy storage devices. By using suction and pressing instead of heat to remove water from nanocellulose mixtures, the energy consumption and costs can be reduced by more than 95 percent.
A new pilot study conducted by researchers at RISE Research Institutes of Sweden shows that heating costs can be reduced by 95 to 99 percent, by using suction and pressing in a roll-to-roll process when producing films from nanocellulose. The study is based on the Digital Cellulose Center’s research, 0-3D project (funded by the Swedish Foundation for Strategic Research), as well as an upscaling project at RISE.
“We hope that our findings will lead to more businesses investing in nanocellulose”, says Karl Håkansson, Senior Research Associate at RISE. With this process, the industry can, in a low-cost and energy-efficient manner, produce high-performing nanocellulose films to replace plastics or to produce tailor-made films needed within biomedical or electronics applications.”
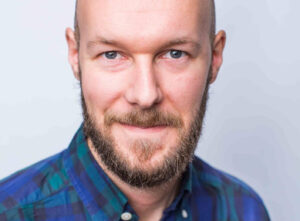
New method removes 95 percent of the water from nanocellulose
In order to limit material focus and aggregates, the nanocellulose is dispersed in water at a low concentration, similar to the papermaking process. The nanocellulose used in the pilot study contained over 99,5 percent water and the biggest challenge when making films from the material is getting rid of the water. The most common way to remove it is by heating to evaporate the water, but this consumes a lot of energy and is therefore expensive, and evaporation is also a slow process.
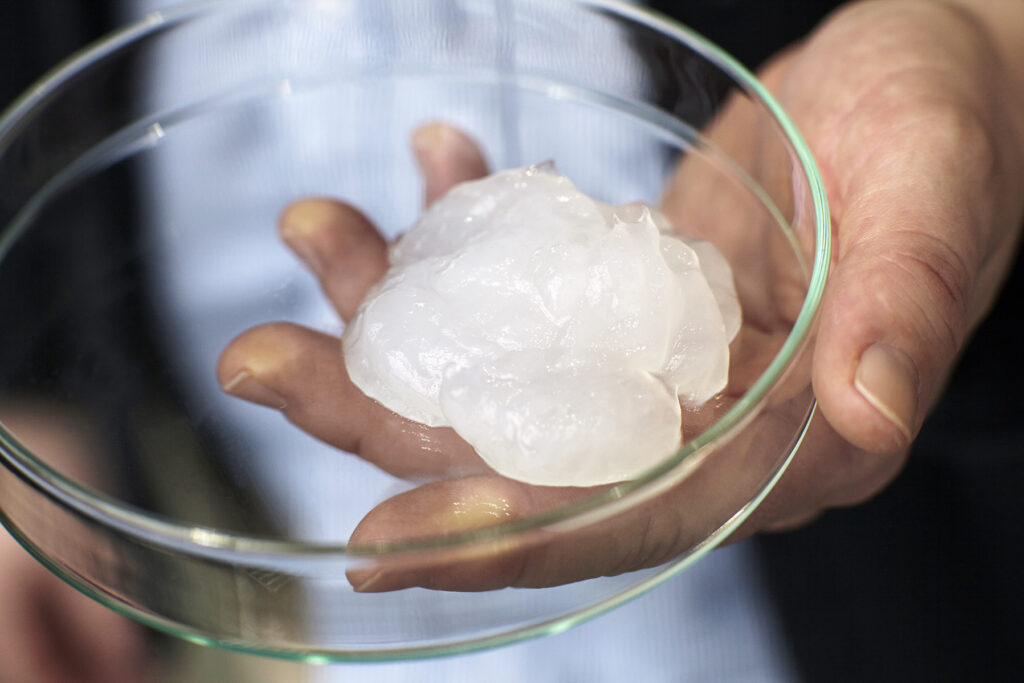
“Nanocellulose has been used for over a decade in developing green electronics like batteries, fuel cells, and sensors”, says Jesper Edberg, researcher at RISE and scientific leader at the Digital Cellulose Center. “However, the road towards commercialization has been hindered largely by the difficulty of producing films on an industrial scale due to slow dewatering and energy-inefficient drying. The new results represent an important step in the scale-up process.”
The new method developed by RISE is based on processes commonly used in papermaking, such as suction and pressing. The first tests remove 95 to 99 percent of the water, resulting in reduced heating cost by the same percentage. The tests were performed at a speed of one meter per minute.
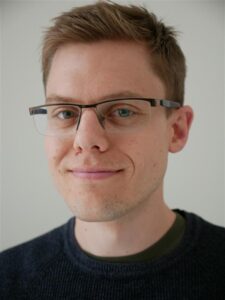
“RISE papermaking pilot-park FENIX can be used to design new or re-design existing papermaking processes, for example towards nanocellulose film production as was the case here”, says RISE researcher Karl Håkansson. “The next step is to tune the film production process to suit different nanocellulose grades, applications, and products. We are now looking for industrial partners that want to test the manufacturing method for their products.”
The idea of the manufacturing method started as an accident, Karl Håkansson continues:
“When cleaning up spilled nanocellulose in the lab with a paper tissue, we noticed that the tissue was very efficient at absorbing the water from the nanocellulose. We then asked ourselves if a water-absorbing material can be used to remove water from nanocellulose dispersions, and the answer was yes.”
Nanocellulose films can replace plastics and conduct ions
Nanocellulose is the umbrella term for a range of different nanoparticles, such as cellulose nanofibrils, microfibrillated cellulose, and cellulose nanocrystals which have been around since the early 1980s. The material is usually derived from wood fibers, it is exceptionally strong and completely renewable. Early attempts to produce nanocellulose on a commercial scale failed due to the manufacturing process being very energy-intensive. This issue was for the most part solved more than a decade ago, however, nanocellulose films have faced the same problem since removing water by heat is very energy demanding.
With society’s drive towards a bio-based economy and legislation becoming stricter with regards to single-use plastics, nanocellulose films are an excellent alternative to conventional plastics. It is also predicted to be useful in a range of different fields, from biomedical and bio-based electronics applications to hygiene products and packaging. Nanocellulose films are versatile and can for example be used as an absorbing material, a protective barrier e.g., oxygen or grease, a substrate for printed electronics, and even in energy storage devices.
Karl Håkansson continues:
“What is exciting about the method is that the raw material, cellulose from the forest is renewable, in combination with the process being both cheaper and more energy-efficient than heating makes this process unique and opens up new possibilities for the industry. Our hope is that this will lead to more renewable products on the market made from nanocellulose.”